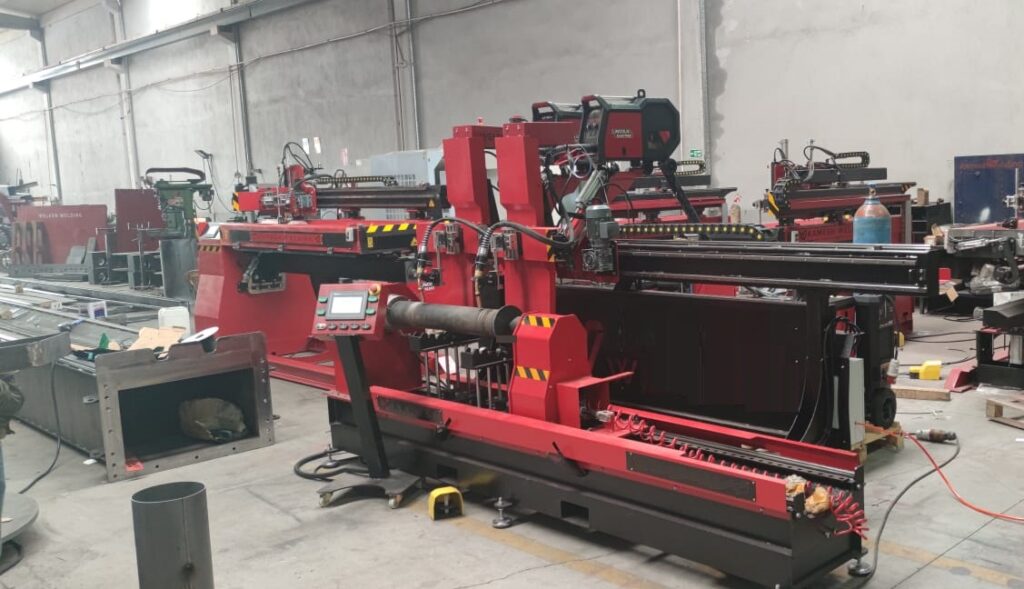
Laser cutting and welding machines are used to cut and weld materials using a high-powered laser beam. Laser cutting machines use the laser beam to melt or vaporize the material, while laser welding machines use the laser beam to heat the material to its melting point, causing it to fuse together.
Laser cutting and welding machines can be used to cut and weld a wide variety of materials, including metals, plastics, and ceramics. They are used in a wide variety of industries, including automotive, electronics, aerospace, and medical devices.
Laser cutting
Laser cutting machines are used to cut materials into precise shapes. The laser beam is typically focused through a nozzle to create a narrow beam of high-intensity light. The laser beam is then directed onto the material, where it melts or vaporizes the material.
Laser cutting machines can be used to cut a wide variety of materials, including:
- Metals: steel, aluminum, stainless steel, brass, copper, titanium, etc.
- Plastics: acrylic, polycarbonate, ABS, PVC, etc.
- Ceramics: glass, alumina, zirconia, etc.
Laser cutting machines are used in a wide variety of industries, including:
- Automotive: laser cutting is used to cut automotive parts, such as car doors, hoods, and fenders.
- Electronics: laser cutting is used to cut electronic components, such as circuit boards and semiconductors.
- Aerospace: laser cutting is used to cut aerospace components, such as aircraft fuselages and engine parts.
- Medical devices: laser cutting is used to cut medical devices, such as stents and implants.
Laser welding
Laser welding machines are used to weld materials together. The laser beam is typically focused through a nozzle to create a narrow beam of high-intensity light. The laser beam is then directed onto the materials to be welded, where it heats the materials to their melting point, causing them to fuse together.
Laser welding machines can be used to weld a wide variety of materials, including:
- Metals: steel, aluminum, stainless steel, brass, copper, titanium, etc.
- Plastics: acrylic, polycarbonate, ABS, PVC, etc.
- Ceramics: glass, alumina, zirconia, etc.
Laser welding machines are used in a wide variety of industries, including:
- Automotive: laser welding is used to weld automotive parts, such as car doors, hoods, and fenders.
- Electronics: laser welding is used to weld electronic components, such as circuit boards and semiconductors.
- Aerospace: laser welding is used to weld aerospace components, such as aircraft fuselages and engine parts.
- Medical devices: laser welding is used to weld medical devices, such as stents and implants.
Benefits of laser cutting and welding machines
Laser cutting and welding machines offer a number of benefits over traditional cutting and welding methods, including:
- Precision: Laser cutting and welding machines can produce very precise cuts and welds. This is because the laser beam can be focused to a very small spot size.
- Speed: Laser cutting and welding machines are very fast. This is because the laser beam can be moved at a high speed.
- Versatility: Laser cutting and welding machines can be used to cut and weld a wide variety of materials.
- Automation: Laser cutting and welding machines can be automated to perform complex tasks without the need for human intervention.
Overall, laser cutting and welding machines are versatile and efficient tools for cutting and welding a wide variety of materials. They are used in a wide variety of industries and can offer a number of benefits over traditional cutting and welding methods.
Automation in Laser Cutting and Welding Machines
Automation is playing an increasingly important role in laser cutting and welding machines. Automated laser cutting and welding machines offer a number of benefits, including:
- Increased efficiency: Automated laser cutting and welding machines can significantly increase the efficiency of production by automating repetitive tasks, such as loading and unloading materials, positioning the laser head, and cutting or welding parts.
- Improved quality: Automated laser cutting and welding machines can help to improve the quality of products by ensuring that parts are cut or welded consistently and accurately.
- Reduced labor costs: Automated laser cutting and welding machines can help to reduce labor costs, especially for repetitive tasks.
- Improved safety: Automated laser cutting and welding machines can help to improve the safety of workers by reducing the need for workers to perform dangerous tasks, such as working near high-power lasers and hot metal.
Here are some specific examples of how automation is being used in laser cutting and welding machines:
- Automated loading and unloading: Automated laser cutting and welding machines can be equipped with automated loading and unloading systems. This allows the machines to operate unattended, which can further increase efficiency and reduce labor costs.
- Automated positioning: Automated laser cutting and welding machines can be equipped with automated positioning systems. This allows the machines to precisely position the laser head, which ensures that parts are cut or welded accurately.
- Automatic process control: Automated laser cutting and welding machines can be equipped with automatic process control systems. This allows the machines to monitor and control the cutting or welding process, which ensures that parts are cut or welded to the correct specifications.
Automated laser cutting and welding machines are used in a wide variety of industries, including:
- Automotive industry: Automated laser cutting and welding machines are used in the automotive industry to cut and weld parts for cars, trucks, and other vehicles.
- Electronics industry: Automated laser cutting and welding machines are used in the electronics industry to cut and weld circuit boards and other electronic components.
- Food and beverage industry: Automated laser cutting and welding machines are used in the food and beverage industry to cut and weld packaging materials.
- Medical device industry: Automated laser cutting and welding machines are used in the medical device industry to cut and weld medical devices, such as pacemakers and stents.
- Consumer goods industry: Automated laser cutting and welding machines are used in the consumer goods industry to cut and weld a wide variety of consumer goods, such as toys, appliances, and household products.
The use of automation in laser cutting and welding machines is expected to grow in the coming years. As automation technology continues to develop, we can expect to see even more innovative and sophisticated automated laser cutting and welding solutions in the future.
Automated Loading and Unloading for Laser Cutting Machines
Automated loading and unloading is a key feature of many automated laser cutting and welding machines. Automated loading and unloading systems can help to increase the efficiency, productivity, and safety of laser cutting and welding operations.
There are a number of different types of automated loading and unloading systems available for laser cutting and welding machines. Some of the most common types include:
- Robotic loading and unloading systems: Robotic loading and unloading systems use robots to load and unload materials from the laser cutting or welding machine. Robotic loading and unloading systems are very versatile and can be used to handle a wide variety of materials and shapes.
- Conveyor belt loading and unloading systems: Conveyor belt loading and unloading systems use conveyor belts to transport materials to and from the laser cutting or welding machine. Conveyor belt loading and unloading systems are ideal for handling large volumes of materials.
- Pallet loading and unloading systems: Pallet loading and unloading systems use pallets to load and unload materials from the laser cutting or welding machine. Pallet loading and unloading systems are ideal for handling heavy or bulky materials.
Automated loading and unloading systems offer a number of benefits, including:
- Increased efficiency: Automated loading and unloading systems can help to significantly increase the efficiency of laser cutting and welding operations by eliminating the need for manual loading and unloading.
- Improved productivity: Automated loading and unloading systems can help to improve the productivity of laser cutting and welding operations by allowing the machines to operate continuously.
- Reduced labor costs: Automated loading and unloading systems can help to reduce labor costs, especially for repetitive tasks.
- Improved safety: Automated loading and unloading systems can help to improve the safety of workers by reducing the need for workers to perform dangerous tasks, such as working near high-power lasers and hot metal.
Automated loading and unloading systems are becoming increasingly popular for laser cutting and welding machines. As the cost of automation technology continues to decrease, we can expect to see even more laser cutting and welding machines equipped with automated loading and unloading systems in the future.
Here are some specific examples of automated loading and unloading systems that are used with laser cutting and welding machines:
- FANUC Arc Mate 100iD robot: The FANUC Arc Mate 100iD robot is a six-axis robot that can be used to load and unload materials from laser cutting and welding machines. The Arc Mate 100iD is a popular choice for automated loading and unloading because it is fast, accurate, and reliable.
- ABB IRB 1600 robot: The ABB IRB 1600 robot is another six-axis robot that can be used to load and unload materials from laser cutting and welding machines. The IRB 1600 is similar to the Arc Mate 100iD in terms of its capabilities and performance.
- KUKA KR 16 L robot: The KUKA KR 16 L robot is a lightweight robot that is ideal for automated loading and unloading of small and delicate parts. The KR 16 L is fast, accurate, and easy to program.
Automated loading and unloading systems are an essential part of many automated laser cutting and welding machines. Automated loading and unloading systems can help to improve the efficiency, productivity, safety, and cost-effectiveness of laser cutting and welding operations.
Automated Positioning
Automated positioning is a key feature of many automated laser cutting and welding machines. Automated positioning systems help to ensure that the laser head is precisely positioned relative to the workpiece, which results in high-quality cuts and welds.
There are a number of different types of automated positioning systems available for laser cutting and welding machines. Some of the most common types include:
Camera-based positioning systems: Camera-based positioning systems use cameras to identify and track the workpiece. The camera data is then used to control the movement of the laser head. Camera-based positioning systems are very accurate and can be used to position the laser head even in complex geometries.
Laser-based positioning systems: Laser-based positioning systems use lasers to measure the distance between the laser head and the workpiece. The laser data is then used to control the movement of the laser head. Laser-based positioning systems are very fast and can be used to position the laser head at very high speeds.
Encoder-based positioning systems: Encoder-based positioning systems use encoders to track the movement of the laser head. The encoder data is then used to control the movement of the laser head. Encoder-based positioning systems are very reliable and can be used to position the laser head with high accuracy.
Automated positioning systems offer a number of benefits, including:
- Improved accuracy: Automated positioning systems help to ensure that the laser head is precisely positioned relative to the workpiece, which results in high-quality cuts and welds.
- Increased speed: Automated positioning systems can help to increase the speed of laser cutting and welding operations by allowing the laser head to be positioned more quickly and accurately.
- Reduced waste: Automated positioning systems can help to reduce waste by ensuring that the laser head is always positioned correctly.
- Improved safety: Automated positioning systems can help to improve safety by reducing the need for workers to work near high-power lasers and hot metal.
Automated positioning systems are becoming increasingly common in laser cutting and welding machines. As the cost of automation technology continues to decrease, we can expect to see even more laser cutting and welding machines equipped with automated positioning systems in the future.
Here are some specific examples of automated positioning systems that are used with laser cutting and welding machines:
- Precitec Proscan: The Precitec Proscan is a camera-based positioning system that is designed for laser cutting and welding machines. The Proscan is very accurate and can be used to position the laser head in complex geometries.
- Scanlab IntelliSCAN: The Scanlab IntelliSCAN is another camera-based positioning system that is designed for laser cutting and welding machines. The IntelliSCAN is similar to the Proscan in terms of its capabilities and performance.
- Raycus SmartScan: The Raycus SmartScan is a laser-based positioning system that is designed for laser cutting and welding machines. The SmartScan is very fast and can be used to position the laser head at very high speeds.
Automated positioning systems are an essential part of many automated laser cutting and welding machines. Automated positioning systems can help to improve the accuracy, speed, waste reduction, and safety of laser cutting and welding operations.
Automatic Process Control
Automatic process control is a system that uses sensors and software to monitor and control the laser cutting and welding process. Automatic process control systems can help to improve the quality, consistency, and efficiency of laser cutting and welding operations.
Automatic process control systems typically work by monitoring the following parameters:
- Laser power: The laser power is the amount of energy that is being delivered to the workpiece. Automatic process control systems can adjust the laser power to ensure that the cut or weld is being made at the correct speed and temperature.
- Laser speed: The laser speed is the speed at which the laser head is moving across the workpiece. Automatic process control systems can adjust the laser speed to ensure that the cut or weld is being made at the correct depth.
- Focus: The focus of the laser beam is the point at which the laser beam is most concentrated. Automatic process control systems can adjust the focus of the laser beam to ensure that the cut or weld is being made at the correct location.
- Gas flow: The gas flow is the amount of gas that is being used to protect the workpiece from oxidation. Automatic process control systems can adjust the gas flow to ensure that the cut or weld is being made in a clean environment.
Automatic process control systems can also use sensors to monitor the quality of the cut or weld. For example, a sensor can be used to measure the thickness of the cut or the strength of the weld. If the sensor detects that the cut or weld is not meeting the desired specifications, the automatic process control system can automatically adjust the laser power, speed, focus, or gas flow to correct the problem.
Automatic process control systems offer a number of benefits, including:
- Improved quality: Automatic process control systems can help to improve the quality of laser cuts and welds by ensuring that the process is being controlled consistently.
- Increased consistency: Automatic process control systems can help to increase the consistency of laser cuts and welds by compensating for variations in the workpiece material and environmental conditions.
- Increased efficiency: Automatic process control systems can help to increase the efficiency of laser cutting and welding operations by reducing the need for manual intervention.
- Reduced waste: Automatic process control systems can help to reduce waste by ensuring that the laser cuts and welds are being made as efficiently as possible.
Automatic process control systems are becoming increasingly common in laser cutting and welding machines. As the cost of automation technology continues to decrease, we can expect to see even more laser cutting and welding machines equipped with automatic process control systems in the future.
Here are some specific examples of automatic process control systems that are used with laser cutting and welding machines:
- LPKF TruFlow: The LPKF TruFlow is an automatic process control system that is designed for laser cutting machines. The TruFlow uses sensors to monitor the laser power, speed, focus, and gas flow, and it automatically adjusts these parameters to ensure that the cut is made at the correct speed and temperature.
- TRUMPF TruLaser Line 7000: The TRUMPF TruLaser Line 7000 is a laser cutting machine that is equipped with an automatic process control system. The TruLaser Line 7000 uses sensors to monitor the laser power, speed, focus, and gas flow, and it automatically adjusts these parameters to ensure that the cut is made at the correct speed and temperature.
- MECCO Laser Pro2000: The MECCO Laser Pro2000 is a laser welding machine that is equipped with an automatic process control system. The MECCO Laser Pro2000 uses sensors to monitor the laser power, speed, focus, and gas flow, and it automatically adjusts these parameters to ensure that the weld is made at the correct speed and temperature.
Automatic process control systems are an essential part of many automated laser cutting and welding machines. Automatic process control systems can help to improve the quality, consistency, efficiency, and waste reduction of laser cutting and welding operations.